The X-TU Architects agency and the GEPEA laboratory of the University of Nantes (UMR 6144 of the CNRS) with Algosource Technologies, R.F.R, Permasteelisa France, their partners of the SymBio2 consortium, unveil their first prototypes of biological solar collectors using microalgae.
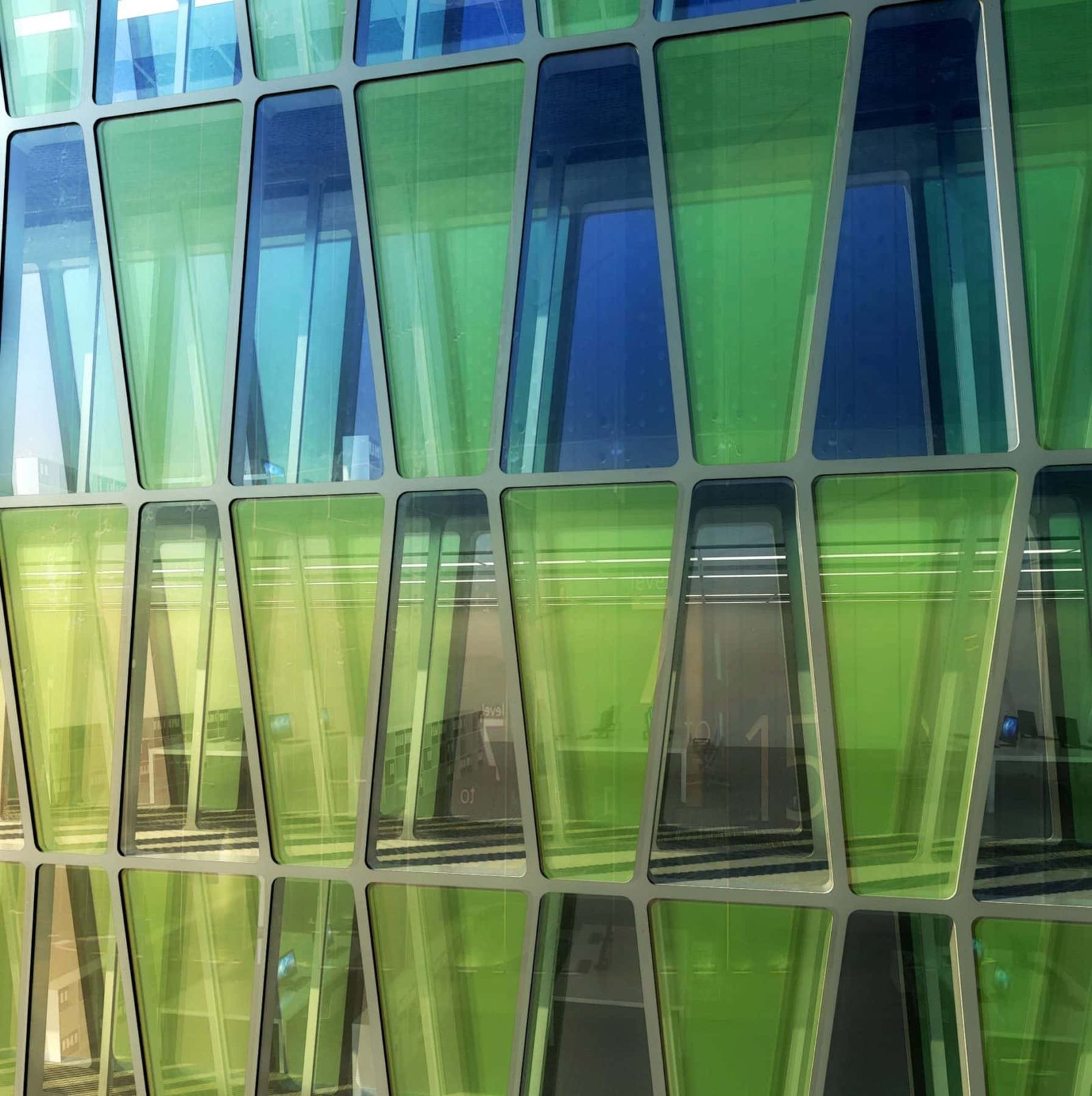
X-TU agency has been working on curtain walls integrating microalgae cultivation since 2007. This concept, born from the observation of peri-urbanization, aims to take advantage of unused facade surfaces to develop microalgae culture. This foodstuff is rich in proteins, lipids (omega-3, omega-6), antioxidants, essential vitamins and natural pigments for both humans and animals. It could also be used in the future as an algae-based fuel or material. A 40% reduction in production costs for the algae industry is possible. In the case of a south-facing facade of a large tower, production is estimated at 33 tonnes of biomass per “vertical hectare”; for the project owner, its payback period is seven years, not counting the image in terms of commitment to sustainable development.

Today, the first prototypes are operational, allowing the behaviour of this culture and the performance of this green façade to be analysed. The consortium has partnered with an industrialist to enable mass production for both new construction and renovation projects. This skin is particularly interesting for high-rise buildings (IGH) as the panels mitigate the overheating effect. It can also be integrated into the building’s water or greywater network. Olivier Scheffer, research director at X-TU, delves deeper into this green façade concept with us.
Kévin Poireau: How do you envisage the maintenance of these panels?
Olivier Scheffer: In this type of photobioreactor (PBR), a system for agitating the medium by injecting pressurised air (known as an “air lift” system) prevents microalgae from adhering to the internal walls (an “antifouling” system). In the rare event of fouling, despite this system, the PBR can be emptied and then injected with pressurised water, with certain detergents in extreme cases, to clean the PBR completely. Finally, in the event of an impact against the glasses, these are laminated and will not allow the liquid to escape. The PBRs are removable and replaceable.
Kévin Poireau: Does this façade system work individually per panel or per façade?
Olivier Scheffer: Each floor is mounted in series, and each PBR can be bypassed in case of a problem.
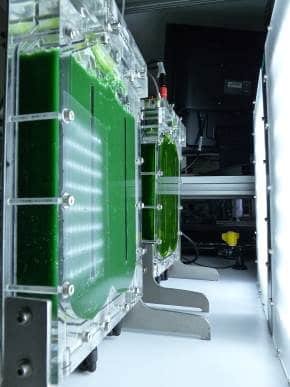
Kévin Poireau: How do you envision “harvesting” these algae? What is the duration of a cycle? What are the optimal conditions for this type of facade? What are its limitations?
Olivier Scheffer: The harvest is carried out on a storey-by-storey basis using a system of pumps and solenoid valves controlled by an industrial PLC, which directs the collection of the filtered algal medium to a technical room in the basement, where it can be pre-conditioned by a technician. The duration of the cycle varies depending on the strain cultivated and the climatic conditions. It ranges from 8 hours to several days. The optimal conditions for the cultivated strains are the same as for humans (hence the interest in associating microalgae cultures with buildings): between 18 and 25°C – even if microalgae are also found in Antarctica or in tropical zones. The current limitations of PBR facades are essentially the cost of thermal regulation. This is a problem we are addressing with our specific patented double-skin biofacade system, which allows for passive thermal regulation of microalgae thanks to the greenhouse effect in winter and natural ventilation in summer, as well as through heat exchange with the building’s water network.
Kévin Poireau: What would be the cost of this type of product compared to more conventional panels with similar thermal performance?
Olivier Scheffer: A large part of our development has focused on the industrialisation of PBRs, in collaboration with our partner Permasteelisa Group, in order to make them simple, robust, low-cost products that are easy to install and maintain. They therefore benefit from the research work of our partner GEPEA (UMR 6144 du CNRS), the world’s leading laboratory (and yes, they are French!) on the controlled culture of microalgae in intensified PBRs, and from the industrial experience of Permasteelisa, synthesised by our agency X-TU and our partner R.F.R (façade consulting firm). The prototypes developed in the laboratory are today the most efficient (at least 50 times more efficient than previous generation PBRs).
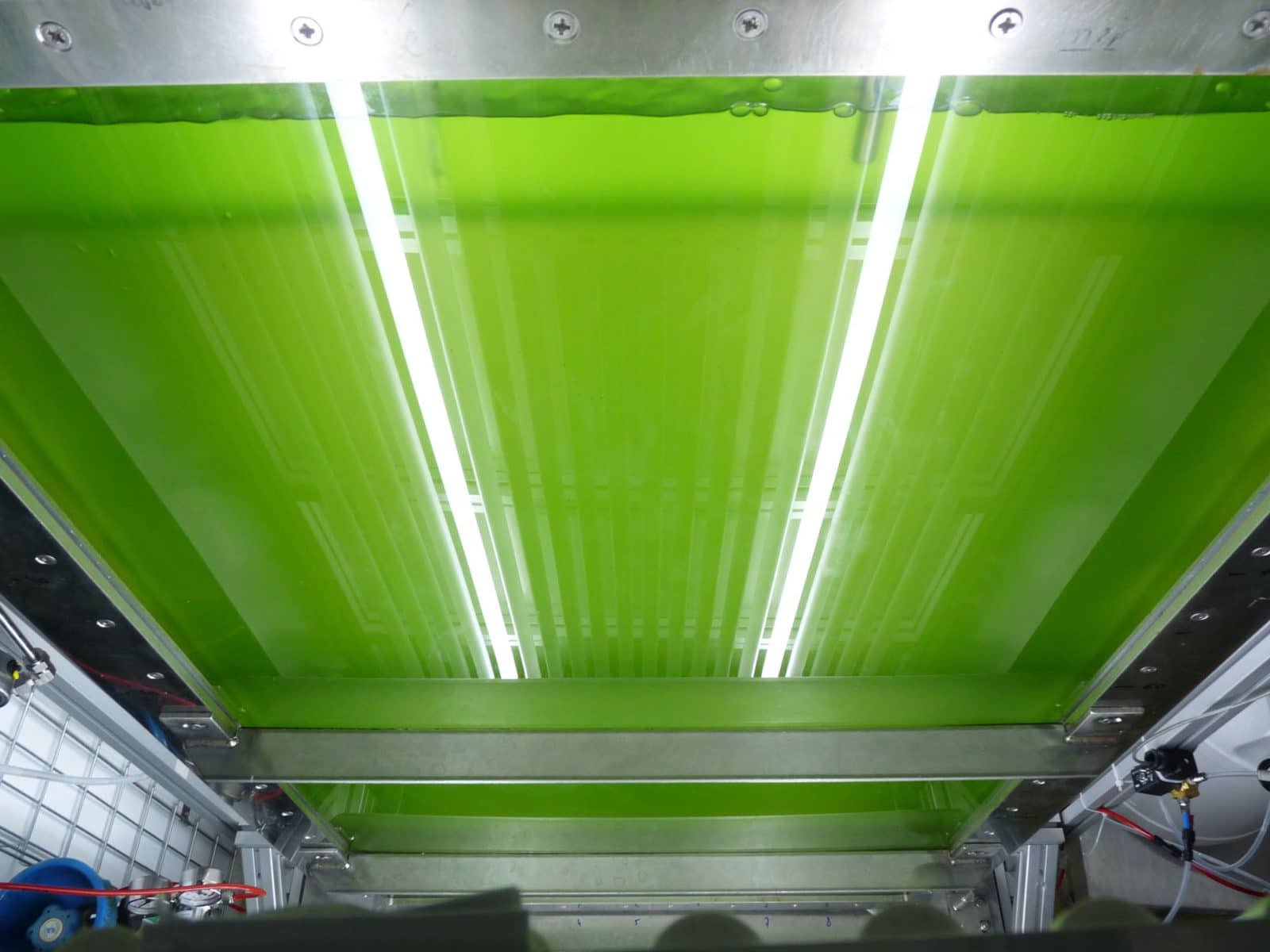
Kévin Poireau: Their characteristics seem to be restrictive (weight, dimensions, how does the glass react), what aesthetic does this provide?
Olivier Scheffer: For aesthetics, I think the rendering demonstrates the good architectural integration of these PBRs. Regarding weight, Permasteelisa sometimes integrates bulletproof glass into its projects that are much heavier. Moreover, PBRs allow 50% of the façade to be made of less expensive glass than on classic curtain wall façades. The glass is sized to manage the weight of the water, which remains limited given the thinness of the PBRs.
Kévin Poireau: What would be the advantages for a developer to grow these algae?
Olivier Scheffer: There are many advantages: thermal regulation of the building from the outside for a low additional cost compared to an HQE façade, profitability of microalgae production on the “green chemistry” application (the profitability announced by some players in the field on algae-based fuels or water treatment are announcements without concrete reality), possibly a rent/lease and therefore a regular income requested from the operator…, not to mention the creation of local industrial jobs and the brand image of a “biotech” building…